Formaldehyde Plant
A higher production yield, flexibility and ease of operation are some of the characteristics that make MAPCO ENGINEERING Formaldehyde Plant the best technical and economical solution.
​
Formaldehyde Plant is the result of the employment of the most advanced, tested and safe technologies applicable to unit operations (catalytic reaction, thermal exchange, absorption, compression etc) and MAPCO ENGINEERING know how grown in many decades of experience carried out in operating worldwide.

MAPCO ENGINEERING equipment are designed according to the "engineering state of art" and the most recognized International Engineering Standards, Codes and Rules used to built Oil Refining and Petrochemical Complex.
The result is a high reliable, low maintenance and easy to operate Plant. This means a high value-for-money plant with a continuous running life not less than 30 years and reduced personnel supervision.
The Process
The process is based on the direct oxidation of methanol by the oxygen contained in a gaseous stream over a ferric molybdate catalyst.
The gaseous formaldehyde resulting from the reaction is then processed in an absorption column where a combination of structured and random packings are used to absorb the gaseous formaldehyde.

The controlled water make-up maintains a fixed formaldehyde concentration, up to 55%. If urea solution is fed instead of water, urea-formaldehyde compound can be produced up to 85%.

The gas coming from the Absorption Column is divided into two streams. The main one is recycled and added to filtered fresh air, the other one is sent to the Catalytic Depuration Unit that virtually eliminates all the contaminants emissions. To this unit are also sent the gaseous effluent coming from the resin plant and the storage tank, if any.



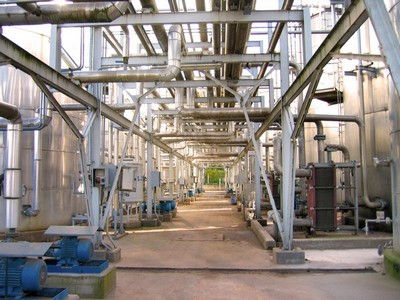
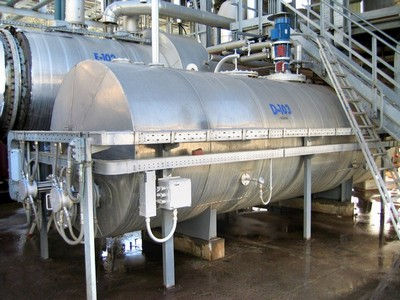

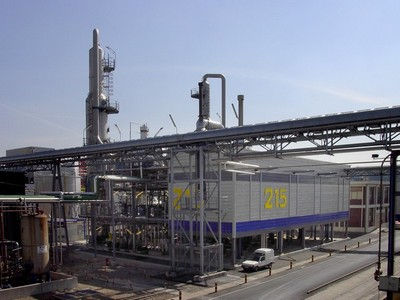
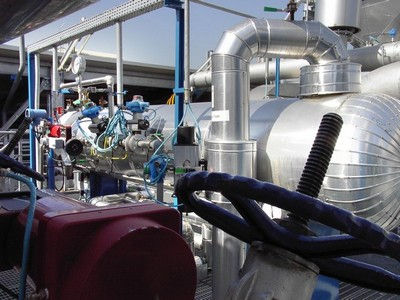











